Understanding the Die Casting Mold Company: A Comprehensive Overview
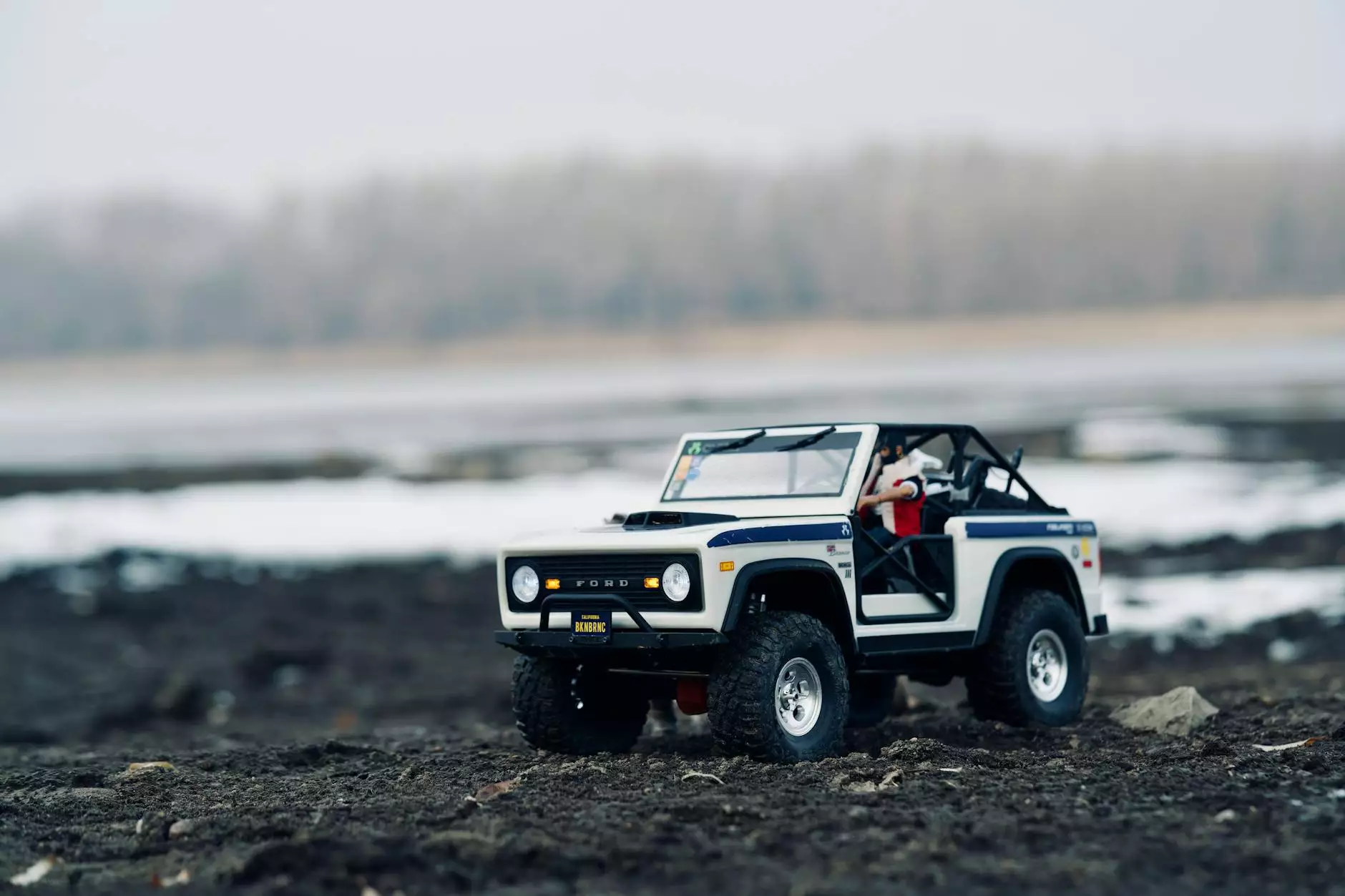
In the realm of manufacturing, the die casting mold company plays a crucial role in the production of high-quality metal components. This process involves a variety of intricate steps and cutting-edge technologies, which we will delve into in this comprehensive article.
What is Die Casting?
Die casting is a metal casting process characterized by forcing molten metal under high pressure into a mold cavity. This method is widely used due to its ability to produce complex shapes with high precision and excellent surface finish. The process is typically used with non-ferrous metals, such as aluminum, zinc, and magnesium.
Advantages of Die Casting
The die casting mold company offers numerous benefits that make it an attractive choice for manufacturers:
- High Precision: Die casting allows for the production of intricate and detailed shapes with tight tolerances.
- Efficient Production: Once the mold is created, high volumes of castings can be produced quickly, reducing lead times.
- Cost-Effectiveness: Although the initial costs of creating a die can be high, the efficiency of the process leads to lower costs per unit for large quantities.
- Material Variety: A die casting mold company can work with various metals, offering flexibility to meet diverse client needs.
- Reduced Waste: The process minimizes material waste, making it more environmentally friendly compared to other methods.
How Die Casting Works
Understanding how die casting works is essential to appreciating its importance in manufacturing. The process involves several critical stages:
1. Design of the Mold
The first step in the die casting process is the design of the mold. Engineers create detailed CAD (Computer-Aided Design) drawings that outline the specifications and features of the desired part.
2. Fabrication of the Mold
After the design phase, the mold is fabricated, usually from high-grade steel. The quality of the mold greatly influences the final product's quality.
3. Melting the Metal
The metal that will be cast is melted in a furnace, prepared to be injected into the mold.
4. Injection of Molten Metal
Molten metal is injected into the mold at high pressure, filling the cavity and forming the desired shapes.
5. Cooling and Ejection
Once the mold is filled, the metal is allowed to cool and solidify. Afterward, the dies are opened, and the cast part is ejected.
6. Finishing Processes
Depending on the application, further processes like machining, coating, or surface treatment may be applied to achieve the desired final product characteristics.
Types of Die Casting Processes
Die casting is classified into two primary processes: hot chamber die casting and cold chamber die casting.
Hot Chamber Die Casting
This method is typically used for metals with low melting points, such as zinc and magnesium. The molten metal is kept in a chamber, allowing for rapid production cycles.
Cold Chamber Die Casting
Cold chamber die casting is used for higher melting point metals, like aluminum. In this process, the molten metal is poured into a chamber before being injected into the mold, making it suitable for more robust applications.
Choosing the Right Die Casting Mold Company
Selecting the right die casting mold company is vital for ensuring the success of your projects. Here are key factors to consider:
- Expertise: Look for a company with extensive experience in die casting, particularly in your industry's specific needs.
- Quality Control: Ensure that the company has stringent quality control measures in place to maintain high standards.
- Technology and Equipment: Modern die casting requires advanced machinery and technologies. Verify that the company uses state-of-the-art equipment.
- Materials Used: They should work with a variety of materials and understand their properties to recommend the best options for your requirements.
- Customer Service: A good die casting mold company should offer excellent customer service, guiding you through the entire process from design to production.
Applications of Die Casting
Die casting is employed across various industries due to its versatility and efficiency. Below are some prominent applications:
Automotive Industry
In the automotive sector, die casting is utilized to create engine blocks, transmission housings, and various other components that require strength and precision.
Consumer Electronics
Die casting is widely used to manufacture casings for consumer electronic devices, ensuring that components are lightweight yet durable.
Aerospace
The aerospace industry benefits from die casting for parts that need to withstand extreme conditions while maintaining a low weight, such as brackets, housings, and fittings.
Medical Devices
In the medical field, precision is critical, and die casting is used to produce various medical components that must conform to strict regulatory standards.
Future of Die Casting
As technology evolves, the die casting mold company sector is poised for innovative advancements. Here are some trends shaping the future:
- Automation: Increased automation in die casting processes will lead to greater efficiency and reduced labor costs.
- Sustainability: Companies are focusing on sustainable practices, including recycling scrap and reducing energy consumption in production.
- Advanced Materials: Ongoing research into new materials will expand the possibilities for die casting applications.
- 3D Printing: The integration of 3D printing technology for prototyping molds offers faster turnaround times and innovative design possibilities.
Conclusion
In conclusion, the die casting mold company serves an integral role in modern manufacturing, providing essential services across various industries. With its numerous advantages, including high precision, efficiency, and cost-effectiveness, die casting is an invaluable process for businesses looking to meet their production needs. By understanding the intricacies of die casting, businesses can make informed decisions when selecting a partner and harnessing the power of this remarkable manufacturing process.
For businesses exploring die casting options, consider deepmould.net, a leading name in the industry known for its high-quality standards and customer-centric approach.