The Impact of Injection Factory on Modern Business
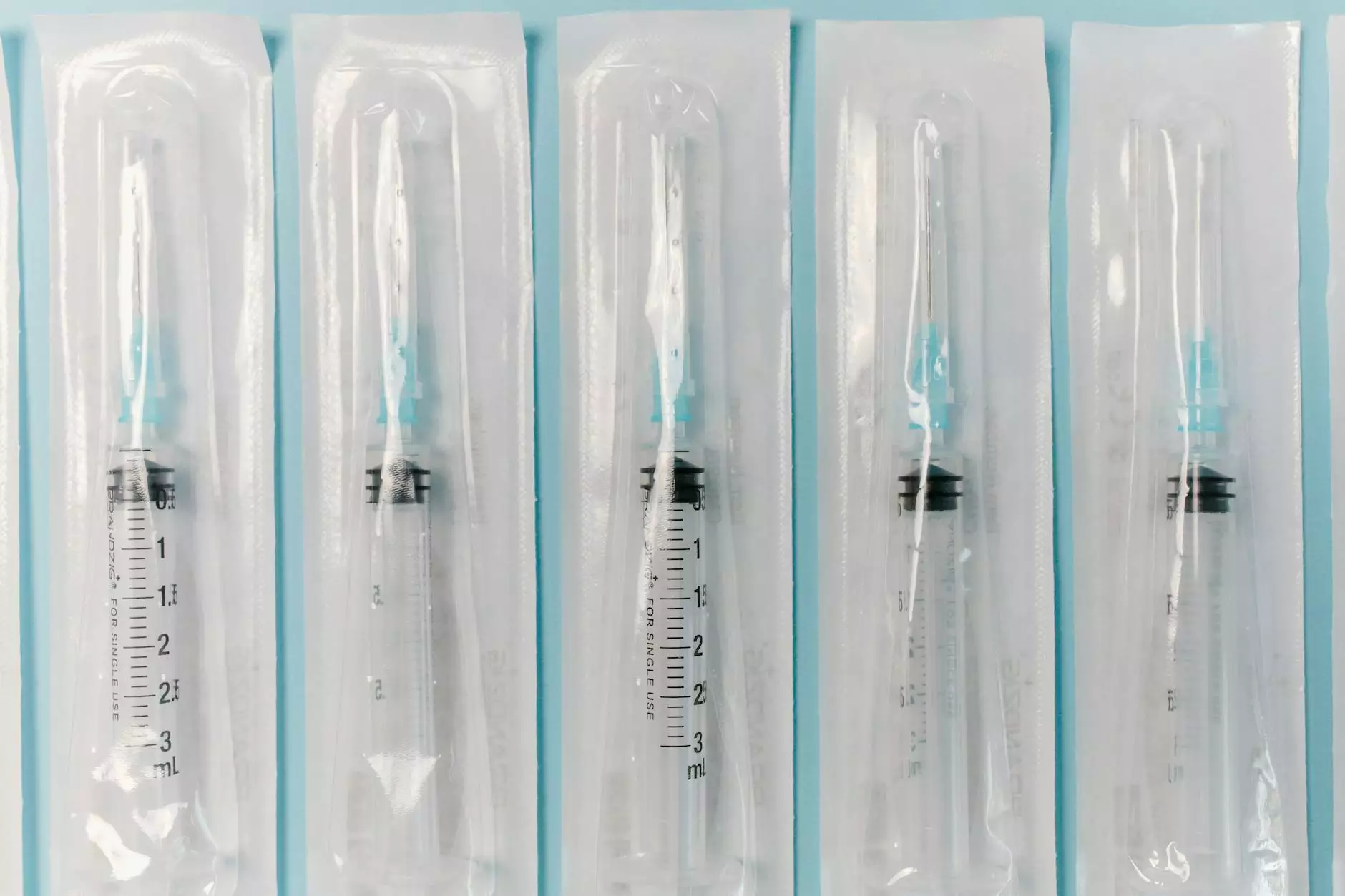
The business world is constantly evolving, and with it, the technologies that drive it forward. One of the most significant transformations has been seen in the realms of art supplies, product design, and 3D printing. Central to this revolution is the concept of the injection factory. This article delves into the profound effects that injection factories have on various industries, highlighting their importance, innovations, and contributions to modern business practices.
Understanding the Concept of an Injection Factory
At its core, an injection factory refers to a facility focused on the manufacturing of products through the injection molding process. This technique involves injecting molten material into a mold to create products with precision and efficiency. The following sections will detail how these factories operate and their vital role in multiple industries.
What is Injection Molding?
Injection molding is a manufacturing process used for producing parts by injecting molten material into a mold. It is commonly utilized for making items from plastics, metals, glass, and more. The process offers several advantages:
- High Efficiency: Once the mold is created, large quantities of products can be manufactured quickly.
- Precision: Injection molding allows for tight tolerances and complex shapes, enhancing product design capabilities.
- Cost-Effectiveness: Although the initial cost for mold creation can be high, the long-term savings from mass production are significant.
- Material Versatility: A wide variety of materials can be used, which can tailor products to specific applications.
Significance of Injection Factories in Business
Injection factories serve as cornerstones in various sectors, enabling businesses to boost productivity while maintaining quality. Below we explore how they impact specific categories relevant to your domain, arti90.com.
1. Revolutionizing Art Supplies
In the realm of art supplies, injection factories play a crucial role in producing high-quality tools and materials for artists. From paint tubes to brushes and sculpting tools, the precision provided by injection molding allows for:
- Enhanced Durability: Products are produced with robust materials that can withstand extensive use.
- Consistency: Each batch of supplies maintains the same quality, ensuring artists receive reliable products.
- Innovative Designs: Artists can benefit from unique shapes and features incorporated into products, enhancing their creative process.
Moreover, as environmental concerns grow, many injection factories are adapting by using sustainable materials in their production processes, fostering eco-friendly practices that resonate with today’s consumers.
2. Advancements in Product Design
Effective product design hinges on the ability to prototype and manufacture efficiently. Injection factories equip designers with the tools necessary to create high-performance products that are not only functional but also aesthetically pleasing. The benefits of leveraging injection factories in product design include:
- Speed to Market: Rapid prototyping via injection molding allows businesses to test and iterate designs quickly.
- Flexibility: Manufacturers can easily adjust designs based on consumer feedback without incurring significant retooling costs.
- Enhanced Collaboration: Design teams can work closely with manufacturers to create tailored products, resulting in better market alignment.
These factors contribute to a more dynamic product development lifecycle, enabling companies to remain competitive and responsive in today's fast-paced marketplace.
3. Innovations in 3D Printing
3D printing and injection molding are often viewed as separate entities, but they can complement each other effectively. Injection factories are beginning to embrace 3D printing technologies, leading to new horizons in manufacturing. Key innovations include:
- Hybrid Manufacturing: Combining traditional injection molding with 3D printing allows for complex designs that traditional molds may struggle to achieve.
- On-Demand Production: With 3D printing capabilities, businesses can produce items as needed, reducing inventory costs.
- Customization: Personalized products can be produced efficiently, catering to the unique requirements of individual customers.
This synergy is leading to significant advancements in industries that rely on injection factories, providing a flexible and efficient approach to modern manufacturing.
Key Challenges Faced by Injection Factories
While injection factories greatly enhance various industries, they are not without challenges. Understanding these hurdles is crucial for businesses looking to engage with or improve their operations.
1. High Initial Investment
The cost of creating molds for injection molding can be substantial. For small businesses or startups, this may pose a significant financial barrier that could deter entry into the market. Careful financial planning and exploration of loan options may be necessary to mitigate this challenge.
2. Waste Management
Although injection molding is efficient, it can produce waste in the form of scrap materials. Implementing a robust waste management plan is essential to minimize environmental impact and adhere to sustainability goals. This also aligns with the growing consumer demand for eco-friendly manufacturing processes.
3. Technological Training
As technology evolves, training employees in the latest injection molding techniques becomes imperative. Investing in continuous education will ensure that the workforce remains capable and knowledgeable, thereby enhancing product quality and business efficiency.
Future Trends in Injection Factories
The future of injection factories is poised for transformation, driven primarily by technological advancements and changing consumer demands.
1. Sustainability Practices
More injection factories are adopting sustainable practices by using recycled materials and energy-efficient technologies. This trend aligns with global movements toward reducing carbon footprints and promoting environmentally friendly manufacturing methods.
2. Smart Manufacturing
The integration of IoT (Internet of Things) in manufacturing processes enables real-time monitoring and optimization of production lines. This leads to improved quality control and reduced downtime, thus transforming injection factories into smart manufacturing hubs.
3. Artificial Intelligence
AI-driven analytics will soon become commonplace in injection factories, helping to predict maintenance needs and optimize production schedules. This shift will enhance operational efficiency and ultimately lead to better product quality.
Conclusion
In summary, the injection factory stands as a vital component in the modern manufacturing landscape of art supplies, product design, and 3D printing. As businesses continue to embrace advanced manufacturing processes, the injection factory will undoubtedly play a pivotal role in fostering innovation, efficiency, and sustainability. By understanding its functions, challenges, and future trends, companies can harness the power of injection molding to propel their operations forward in an increasingly competitive marketplace.
Explore more about injection factories and their significance in the business world at arti90.com